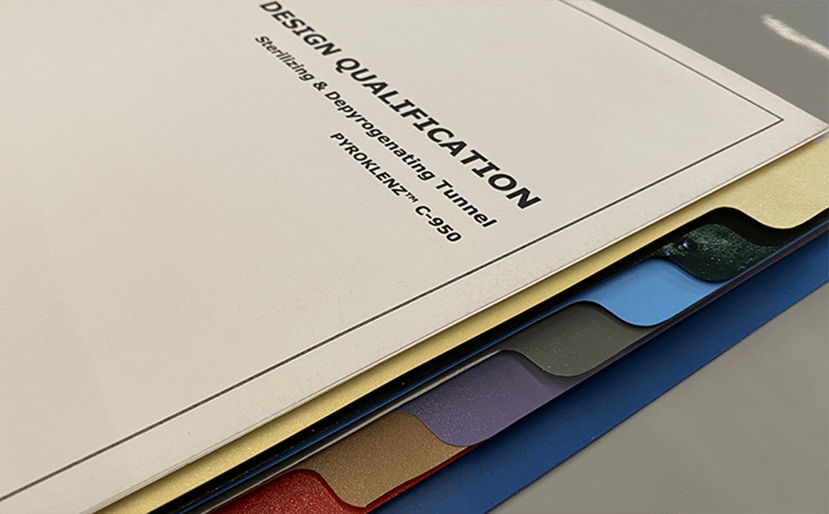
Documentation
Klenzaids works closely with client specifiers and user groups to engineer equipment that will produce reproducible results. Technical documents such as DQ, FS, SDS, HDS, and certificates generated by this established process ensure that SOPs for such equipment are easy to follow and sustainable. Further ensuring that factory acceptance testing is first time right and a fast track to qualification is well in place and can be relied on. This allows a project to meet overall timelines and that research+production commitments are fulfilled on time.
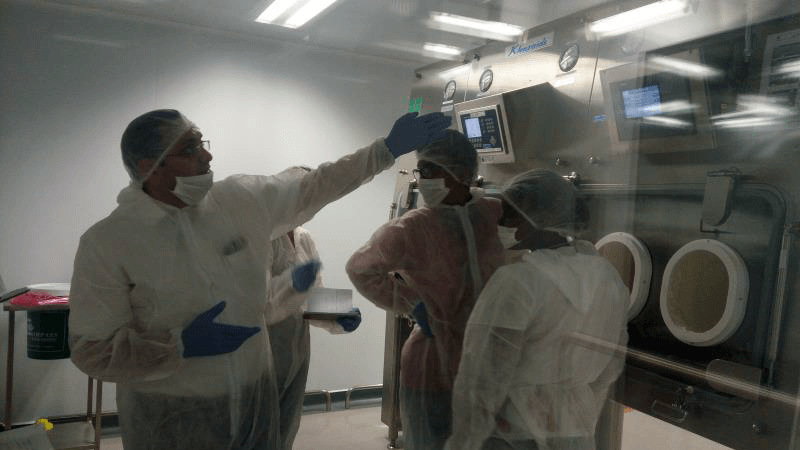
Product Support
It is imperative that requisite support for such facilities and equipment is provided when requested. User groups comprising of operators, principle investigators, production in-charge personnel, project engineers and field technicians invariably need product/facility support in overlapping areas of concern. Klenzaids' product support team is plugged-in constantly trained and updated on trends, regulations and future directions to provide invaluable assistance to clients and their user groups.
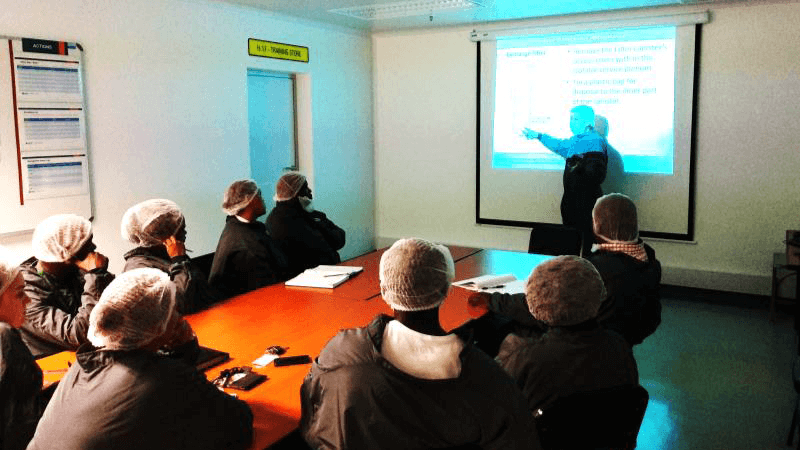
Qualification
Be it a comprehensive turnkey facility/building or a single piece of equipment, Klenzaids' KlenzCare® initiative provides start to end qualification services to clients. The process is initiated with design qualification and related risk assessments and goes through several milestones such as installation qualification, calibration, alarm functions testing, operational qualification and in select cases cycle development and cycle validation where KlenzCare® has a tie up with Valicare® Europe to ensure the highest standard of quality assurance. Klenzaids liaises with client groups and conducts workshops at every step bringing team Klenzaids, client and equipment into a sustainable bond.
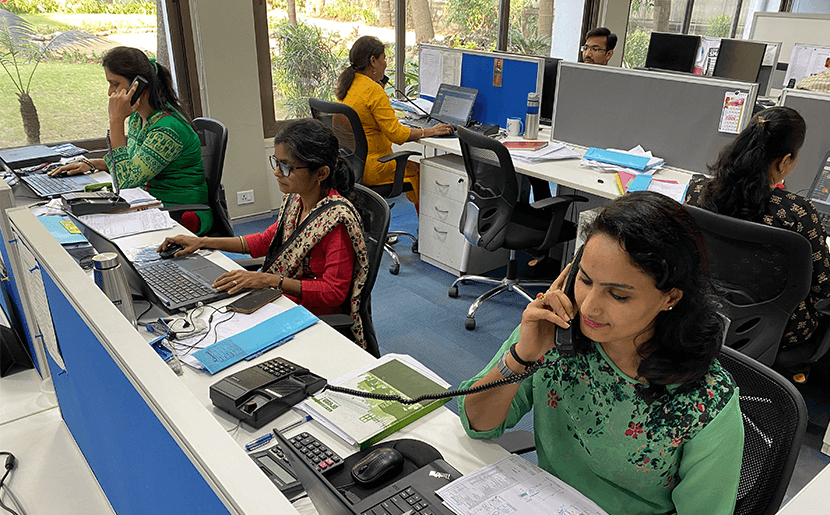
After-Sales Services
Klenzaids provides practical long-term solutions urging users to enter cost-effective comprehensive annual maintenance contracts. In special green-field projects operations and maintenance contracts are also put into effect where the client groups are not staffed to handle the 24/7 demands of such facilities. Each client group under AMC is provided a unique number which can be used to check records and post feedback online.
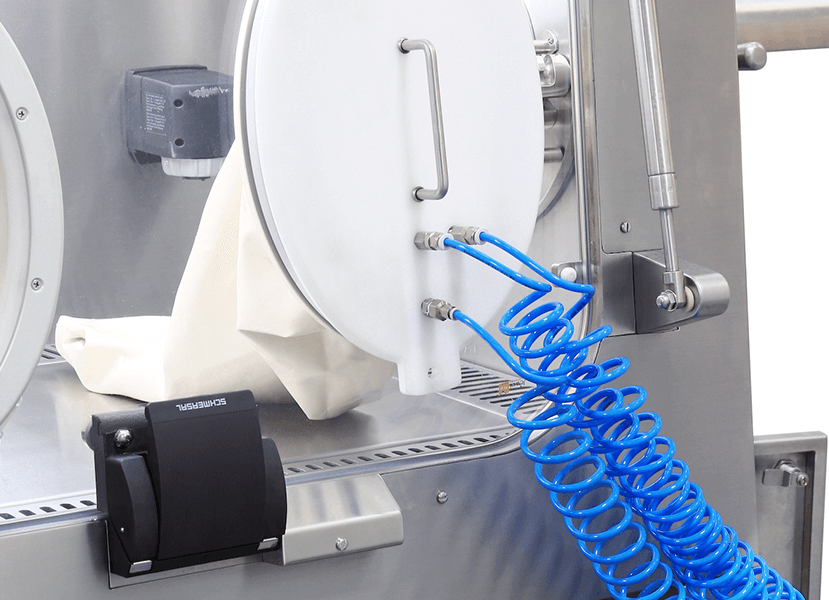
Value Added Service
Going beyond regulatory mandates Klenzaids provides benchmark value added services such as fully customised risk and threat assessments, I/O testing, glove leak testing, RTM, disaster recovery, software & SCADA for building automation etc. Klenzaids also undertakes first of its kind custom projects which often require unique process development in which case qualification services are also customized to benefit from the quality by design paradigm.
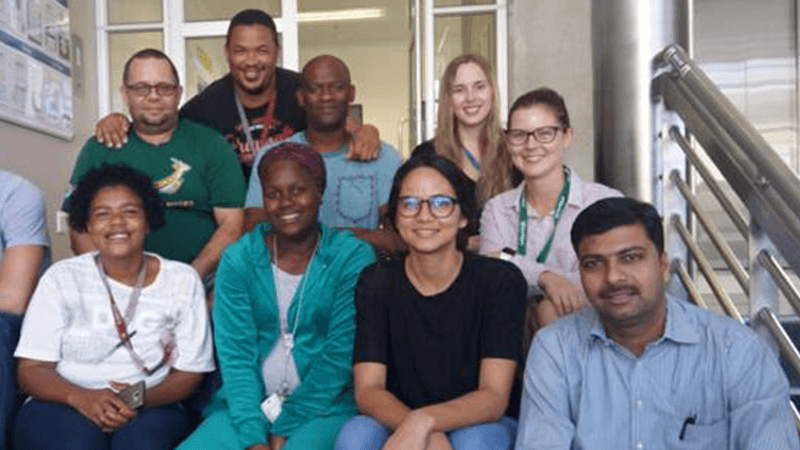
Training
Klenzaids with its industry renowned 1st of its kind in the region, Klenzaids GMP academy has taken training further by ways of the KlenzCare® initiative. Now structured to impart not just training on every aspect of cGMP and cGLP but offering on-site modules aswell. Augmented reality and remote training is also possible. Klenzaids collaborates with Valicare® GmbH to bring global skill sets to solve process and packaging regulatory issues by ways of audits, inspections and related training.
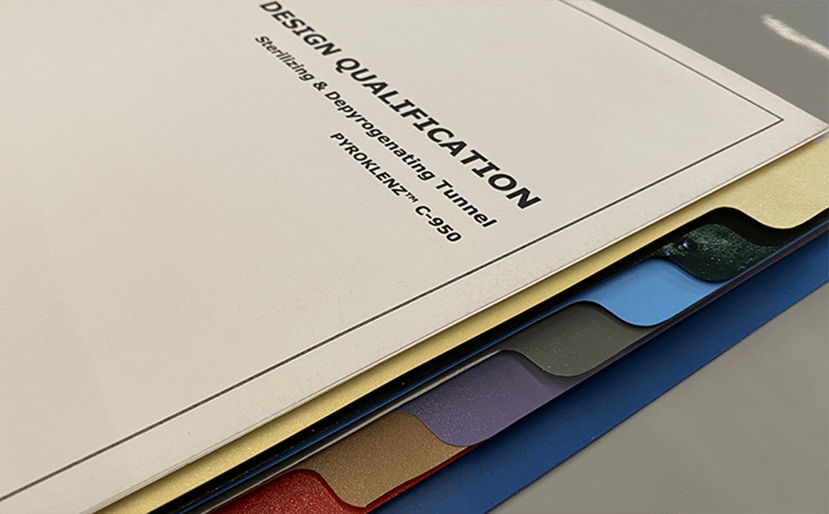
Documentation
Klenzaids works closely with client specifiers and user groups to engineer equipment that will produce reproducible results. Technical documents such as TDQ, FS, SDS, HDS, and certificates generated by this established process ensure that SOPs for such equipment are easy to follow and sustainable. Further ensuring that factory acceptance testing is first time right and a fast track to qualification is well in place and can be relied on. This allows a project to meet overall timelines and that research+production commitments are fulfilled on time.
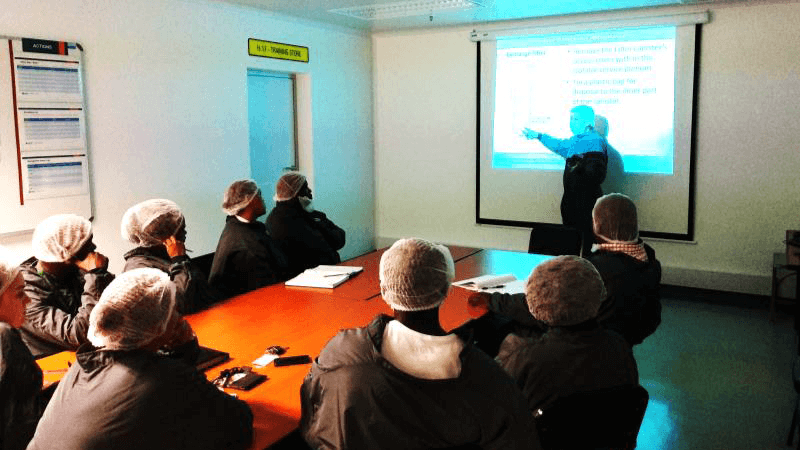
Qualification
Be it a comprehensive turnkey facility/building or a single piece of equipment, Klenzaids' KlenzCare® initiative provides start to end qualification services to clients. The process is initiated with design qualification and related risk assessments and goes through several milestones such as installation qualification, calibration, alarm functions testing, operational qualification and in select cases cycle development and cycle validation where KlenzCare® has a tie up with Valicare® Europe to ensure the highest standard of quality assurance. Klenzaids liaises with client groups and conducts workshops at every step bringing team Klenzaids, client and equipment into a sustainable bond.
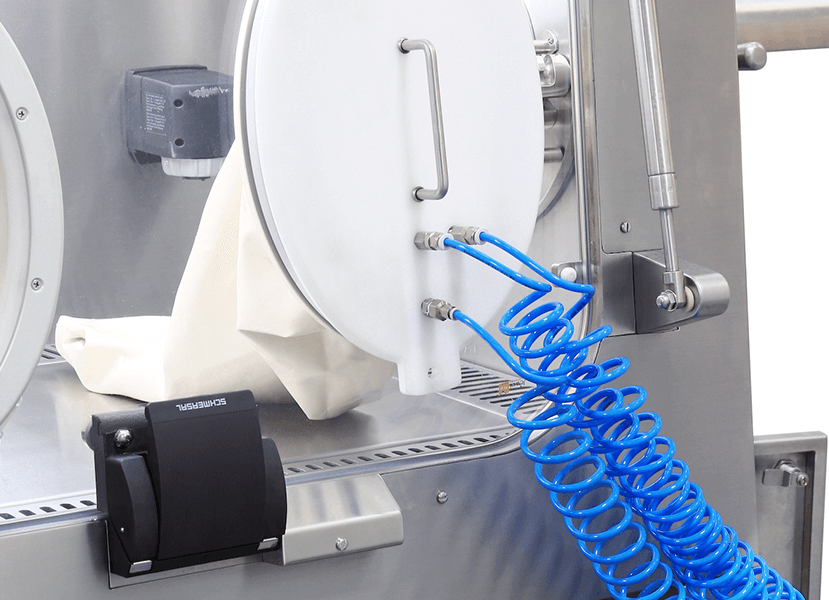
Value Added Service
Going beyond regulatory mandates Klenzaids provides benchmark value added services such as fully customised risk and threat assessments, I/O testing, glove leak testing, RTM, disaster recovery, software & SCADA for building automation etc. Klenzaids also undertakes first of its kind custom projects which often require unique process development in which case qualification services are also customized to benefit from the quality by design paradigm.
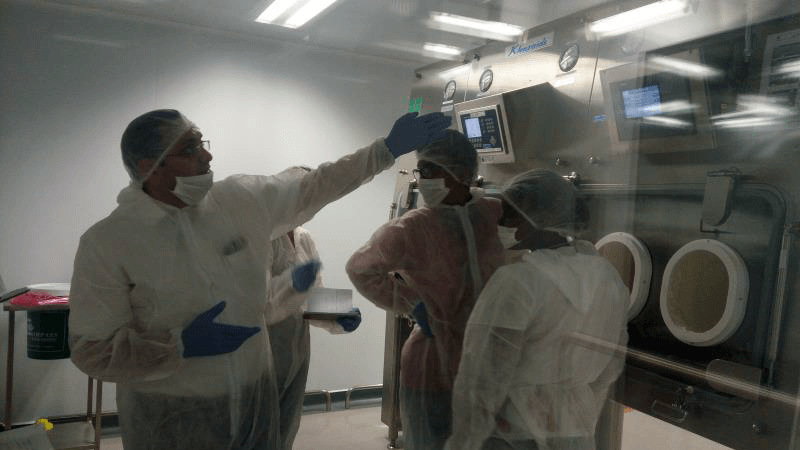
Product Support
It is imperative that requisite support for such facilities and equipment is provided when requested. User groups comprising of operators, principle investigators, production in-charge personnel, project engineers and field technicians invariably need product/facility support in overlapping areas of concern. Klenzaids' product support team is plugged-in constantly trained and updated on trends, regulations and future directions to provide invaluable assistance to clients and their user groups.
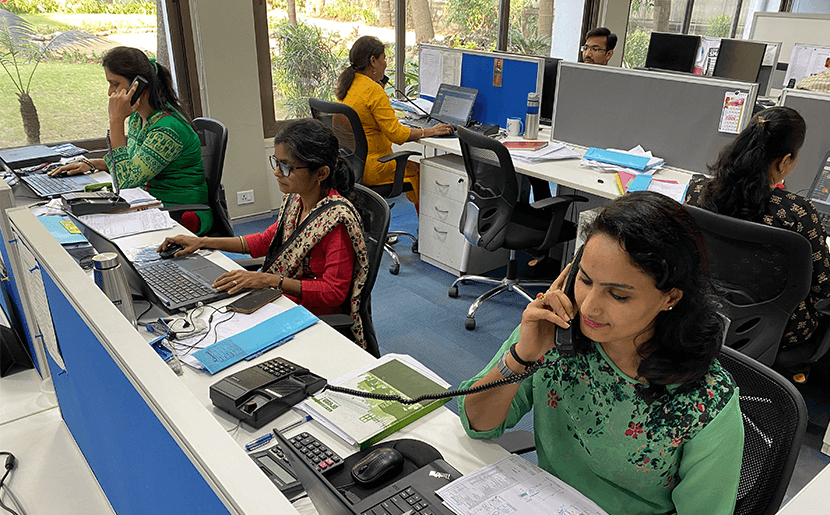
After-Sales Services
Klenzaids provides practical long-term solutions urging users to enter cost-effective comprehensive annual maintenance contracts. In special green-field projects operations and maintenance contracts are also put into effect where the client groups are not staffed to handle the 24/7 demands of such facilities. Each client group under AMC is provided a unique number which can be used to check records and post feedback online.
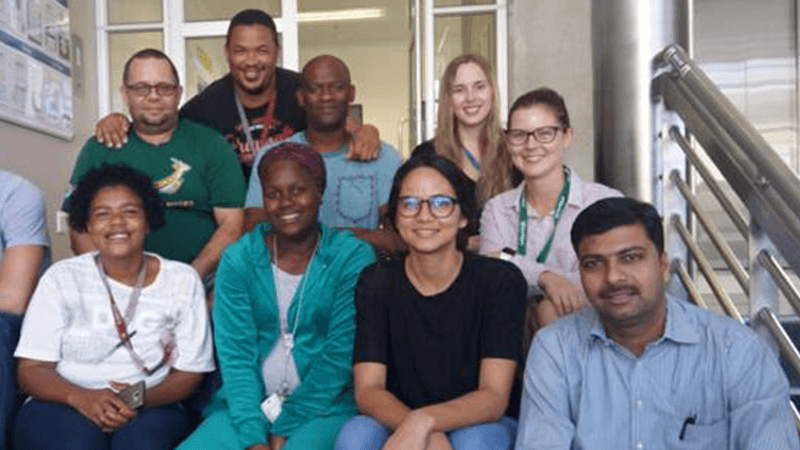
Training
Klenzaids with its industry renowned 1st of its kind in the region, Klenzaids GMP academy has taken training further by ways of the KlenzCare® initiative. Now structured to impart not just training on every aspect of cGMP and cGLP but offering on-site modules aswell. Augmented reality and remote training is also possible. Klenzaids collaborates with Valicare® GmbH to bring global skill sets to solve process and packaging regulatory issues by ways of audits, inspections and related training.